Top 3 Der häufigsten Bestandskontrollrichtlinien
Dieser Blog definiert und vergleicht die drei am häufigsten verwendeten Bestandskontrollrichtlinien. Es sollte sowohl für Neueinsteiger als auch für erfahrene Personen hilfreich sein, die über eine mögliche Änderung der Unternehmenspolitik nachdenken. Der Blog befasst sich auch damit, wie die Bedarfsprognose die Bestandsverwaltung, die Auswahl der zu verwendenden Richtlinie und die Berechnung der Inputs, die diese Richtlinien steuern, unterstützt. Betrachten Sie es als ein abgekürztes Stück Inventar 101.
Szenario
Sie verwalten ein bestimmtes Element. Der Artikel ist für Ihre Kunden wichtig genug, dass Sie genügend Inventar führen möchten, um eine Bevorratung zu vermeiden. Der Artikel ist jedoch auch teuer genug, um den im Inventar gebundenen Bargeldbetrag zu minimieren. Der Prozess der Bestellung von Nachschubbeständen ist so teuer und umständlich, dass Sie auch die Anzahl der Bestellungen minimieren möchten, die Sie generieren müssen. Die Nachfrage nach dem Artikel ist unvorhersehbar. Dies gilt auch für die Vorlaufzeit zwischen dem Zeitpunkt, an dem Sie den Bedarf an mehr feststellen, und dem Zeitpunkt, an dem es gebrauchsfertig oder versandfertig im Regal ankommt.
Ihre Frage lautet “Wie verwalte ich diesen Artikel? Wie entscheide ich, wann ich mehr und wie viel bestellen möchte?” Bei dieser Entscheidung gibt es verschiedene Ansätze, die Sie verwenden können. In diesem Blog werden die am häufigsten verwendeten Richtlinien für die Bestandsplanung beschrieben: Periodische Bestellung bis (T, S), Nachbestellpunkt / Bestellmenge (R, Q) und Min / Max (s, S). Diese Ansätze sind oft in ERP-Systeme eingebettet und ermöglichen es Unternehmen, automatische Vorschläge zu generieren, was und wann bestellt werden soll. Um die richtige Entscheidung zu treffen, müssen Sie wissen, wie jeder dieser Ansätze funktioniert und welche Vorteile und Einschränkungen jeder Ansatz hat.
Periodische Überprüfung, Order-up-to-Richtlinie
Die Kurznotation für diese Richtlinie lautet (T, S), wobei T die feste Zeit zwischen Bestellungen und S die Order-up-to-Level ist.
Wann bestellen: Bestellungen werden wie ein Uhrwerk alle T Tage aufgegeben. Die Verwendung eines festen Nachbestellungsintervalls ist hilfreich für Unternehmen, die ihren Lagerbestand nicht in Echtzeit verfolgen können oder die es vorziehen, Bestellungen in geplanten Intervallen an Lieferanten zu erteilen.
Wie viel zu bestellen ist: Der Lagerbestand wird gemessen und die Lücke zwischen diesem Niveau und der Bestellung bis zur Stufe S berechnet. Wenn der Lagerbestand 7 Einheiten beträgt und S = 10 ist, werden 3 Einheiten bestellt.
Kommentar: Dies ist die am einfachsten zu implementierende Richtlinie, aber auch die am wenigsten agile, um auf Schwankungen der Nachfrage und / oder der Vorlaufzeit zu reagieren. Beachten Sie auch, dass die Auftragsgröße zwar ausreichen würde, um den Lagerbestand auf S zurückzusetzen, wenn der Nachschub sofort erfolgt, in der Praxis jedoch eine gewisse Nachschubverzögerung auftritt, während der der Lagerbestand weiter sinkt, sodass der Lagerbestand selten den ganzen Weg nach oben erreicht S.
Kontinuierliche Überprüfung, Richtlinie für feste Bestellmengen (Nachbestellungspunkt, Bestellmenge)
Die Kurznotation für diese Richtlinie lautet (R, Q), wobei R der Nachbestellungspunkt und Q die feste Bestellmenge ist.
Wann bestellen: Theoretisch wird der Lagerbestand ständig überprüft, in der Praxis wird er jedoch normalerweise regelmäßig zu Beginn oder am Ende eines jeden Arbeitstages überprüft.
Wie viel zu bestellen: Die Bestellgröße ist immer auf Q-Einheiten festgelegt.
Kommentar: (R, Q) reagiert schneller als (S, T), weil es schneller auf Anzeichen eines bevorstehenden Lagerbestands reagiert. Der Wert der festen Bestellmenge Q liegt möglicherweise nicht ganz bei Ihnen. Oft können Lieferanten Bedingungen vorschreiben, die Ihre Q-Auswahl auf Werte beschränken, die mit Minima und Multiples kompatibel sind. Zum Beispiel kann ein Lieferant auf einem Bestellminimum von 20 Einheiten bestehen und immer ein Vielfaches von 5 sein. Daher müssen die Größen entweder 20, 25, 30, 35 usw. sein. (Dieser Kommentar galt auch für die beiden anderen Inventarisierungsrichtlinien.)
Kontinuierliche Überprüfung, Order-up-to-Richtlinie (Min / Max)
Die Kurznotation für diese Richtlinie lautet (s, S), manchmal auch “Little s, big S” genannt, wobei s der Neuordnungspunkt und S die Order-up-to-Ebene ist. Diese Richtlinie wird häufiger als (Min, Max) bezeichnet.
Bestellzeit: Bestellungen werden aufgegeben, sobald der Lagerbestand auf oder unter die Mindestbestellmenge fällt. Wie bei (R, Q) wird der Lagerbestand angeblich ständig überwacht, aber in der Praxis wird er normalerweise am Ende jedes Arbeitstages überprüft.
Wie viel zu bestellen: Die Bestellmenge variiert. Es entspricht der Lücke zwischen dem Maximum und dem aktuellen Inventar in dem Moment, in dem das Minimum erreicht oder überschritten wird.
Kommentar: (Min, Max) reagiert noch besser als (R, Q), da es die Auftragsgröße so anpasst, dass berücksichtigt wird, um wie viel der Lagerbestand unter die Mindestbestellmenge gefallen ist. Wenn die Nachfrage entweder Null oder eine Einheit ist, setzt eine gemeinsame Variation Min = Max -1; Dies wird als “Basisbestand” bezeichnet.”
Eine andere Politik Wahl: Was passiert, wenn ich Lager aus?
Wie Sie sich vorstellen können, wird jede Richtlinie wahrscheinlich zu einer anderen zeitlichen Abfolge von Lagerbeständen führen (siehe Abbildung 1 unten). Es gibt noch einen weiteren Faktor, der beeinflusst, wie sich Ereignisse im Laufe der Zeit abspielen: Die Richtlinie, die Sie für den Umgang mit Lagerbeständen auswählen. Im Großen und Ganzen gibt es zwei Hauptansätze.
Nachbestellrichtlinie: Wenn Sie keinen Vorrat haben, behalten Sie den Überblick über die Bestellung und füllen sie später aus. Im Rahmen dieser Politik ist es sinnvoll, von negativem Inventar zu sprechen. Der negative Lagerbestand stellt die Anzahl der Rückstände dar, die gefüllt werden müssen. Vermutlich erhält jeder Kunde, der gezwungen ist zu warten, die ersten Dibs, wenn der Nachschub eintrifft. Sie haben wahrscheinlich eine Nachbestellrichtlinie für Artikel, die für Ihr Unternehmen einzigartig sind und die Ihr Kunde nicht an anderer Stelle kaufen kann.
Verlustpolitik: Wenn Sie Lagerbestände haben, wendet sich der Kunde an eine andere Quelle, um seine Bestellung auszuführen. Wenn der Nachschub eintrifft, erhalten einige neue Kunden diese neuen Einheiten. Inventar kann niemals unter Null gehen. Wählen Sie diese Richtlinie für Warenartikel, die problemlos von einem Wettbewerber erworben werden können. Wenn Sie es nicht auf Lager haben, wird Ihr Kunde mit Sicherheit woanders hingehen.
Die Rolle der Bedarfsprognose bei der Bestandskontrolle
Die Wahl der Steuerparameter, wie die Werte von Min und Max, erfordert Eingaben aus einer Art Bedarfsprognoseprozess.
Traditionell bedeutete dies, die Wahrscheinlichkeitsverteilung der Anzahl der Einheiten zu bestimmen, die über ein festes Zeitintervall angefordert werden, entweder die Vorlaufzeit in (R, Q) und (Min, Max) Systemen oder T + Vorlaufzeit in (T, S) Systemen. Diese Verteilung wurde als normal angenommen (die berühmte “glockenförmige Kurve”). Traditionelle Methoden wurden erweitert, bei denen die Nachfrageverteilung nicht als normal angenommen wird, sondern als eine andere Verteilung (dh Poisson, negatives Binom usw.)
Diese traditionellen Methoden weisen mehrere Mängel auf.
- Erstens ignoriert es normalerweise das Problem des Unterschreitens, bei dem die Nachfrage das Inventar nicht nur auf den Neuordnungspunkt, sondern darunter senkt. Die Annahme, dass keine Unterschreitung vorliegt, führt zu einer Überschätzung der Servicelevel und der Füllraten.
- Zweitens ist die Wahrscheinlichkeitsverteilung der Nachfrage sehr oft nicht einmal annähernd “glockenförmig” oder wie auch immer die angenommene Verteilung gewählt wurde – insbesondere für Artikel mit intermittierender Nachfrage wie Ersatzteile und Serviceteile.
- Drittens erfordern genaue Schätzungen der Lagerbetriebskosten eine Analyse des gesamten Nachschubzyklus (von einem Nachschub zum nächsten), nicht nur des Teils des Zyklus, der damit beginnt, dass der Bestand den Nachbestellpunkt erreicht.
- Schließlich sind die Vorlaufzeiten für Nachschub in der Regel unvorhersehbar oder zufällig und nicht festgelegt. Viele Modelle gehen von einer festen Vorlaufzeit aus, die auf einer durchschnittlichen, vom Anbieter angegebenen Vorlaufzeit oder einer durchschnittlichen Vorlaufzeit + Sicherheitszeit basiert.
Glücklicherweise gibt es eine bessere Bestandsplanungs- und Bestandsoptimierungssoftware, die auf der Generierung einer Vielzahl zufälliger Nachfrageszenarien zusammen mit zufälligen Vorlaufzeiten basiert. Diese Szenarien “Stresstest” jedes vorgeschlagene Paar von Bestandskontrollparametern und bewerten ihre erwartete Leistung. Benutzer können nicht nur zwischen Richtlinien (z. Min, Max vs. R, Q), sondern auch bestimmen, welche Variation der vorgeschlagenen Richtlinie am besten ist (dh Min, Max von 10,20 vs. 15, 25 usw.) Beispiele für diese Szenarien sind unten angegeben.
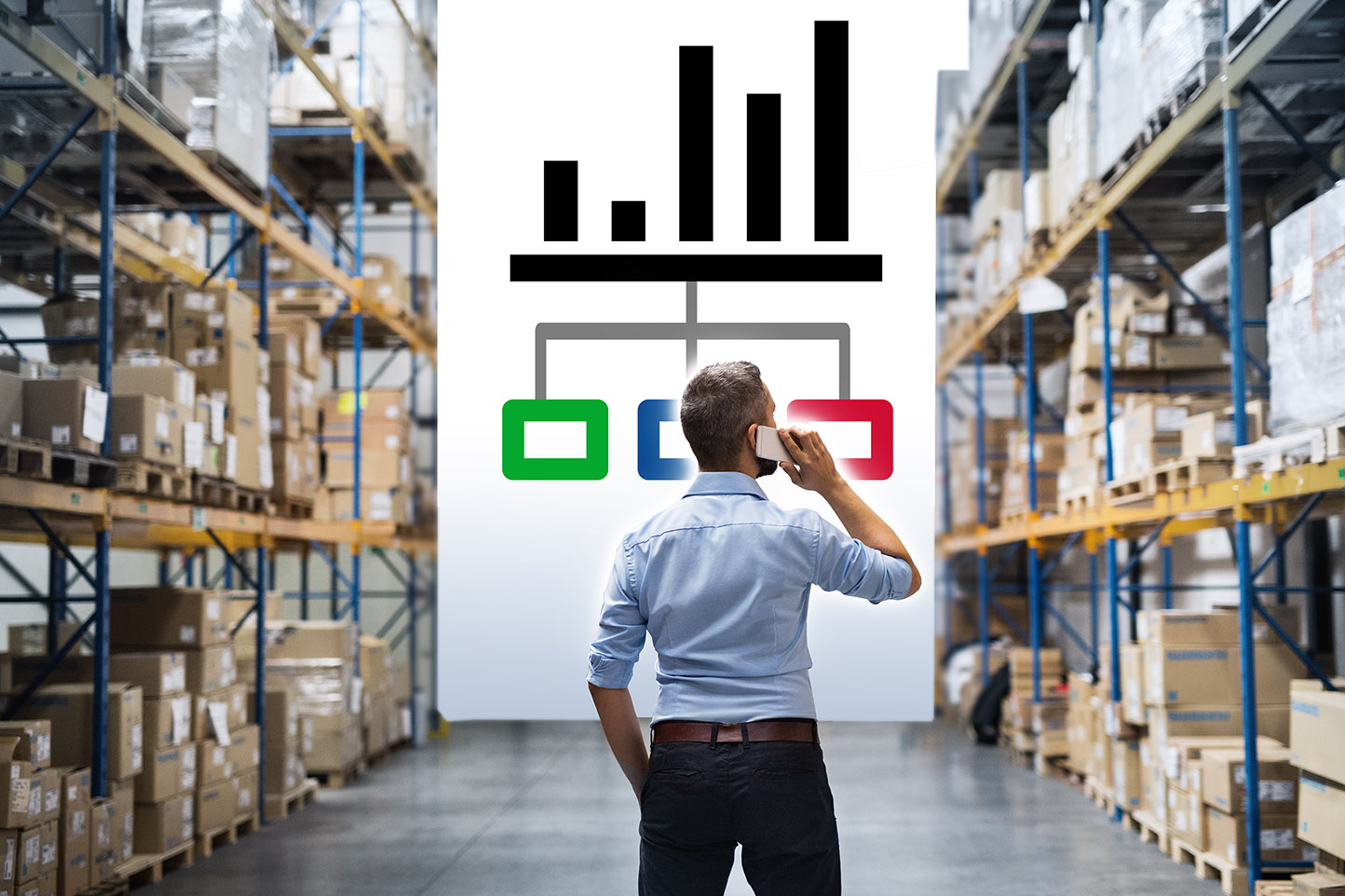
Der Bestellvorgang für Nachschubbestände ist so teuer und umständlich, dass Sie auch die Anzahl der Bestellungen minimieren möchten, die Sie generieren müssen
Auswahl unter Bestandskontrollrichtlinien
Welche Richtlinie ist die richtige für Sie? Es gibt eine klare Hackreihenfolge in Bezug auf die Artikelverfügbarkeit, mit (Min, Max) zuerst, (R, Q) zweitens und (T, S) zuletzt. Diese Reihenfolge ergibt sich aus der Reaktionsfähigkeit der Richtlinie auf Schwankungen der Zufälligkeit von Nachfrage und Nachschub. Die Reihenfolge kehrt sich um, wenn die einfache Implementierung berücksichtigt wird.
Wie “bewerten” Sie die Leistung einer Inventarisierungsrichtlinie? Es gibt zwei gegensätzliche Kräfte, die ausgeglichen werden müssen: Kosten und Service.
Lagerkosten können entweder als Lagerinvestition oder Lagerbetriebskosten ausgedrückt werden. Ersteres ist der Dollarwert der Gegenstände, die darauf warten, verwendet zu werden. Letzteres ist die Summe aus drei Komponenten: Haltekosten (die Kosten für die “Pflege und Fütterung von Sachen im Regal”), Bestellkosten (im Grunde die Kosten für das Schneiden einer Bestellung und das Empfangen dieser Bestellung) und Mangelkosten (die Strafe, die Sie zahlen, wenn Sie entweder einen Verkauf verlieren oder einen Kunden zwingen, auf das zu warten, was er will).
Der Service wird normalerweise anhand des Service Levels und der Füllrate gemessen. Service Level ist die Wahrscheinlichkeit, dass ein angeforderter Artikel sofort ab Lager versandt wird. Die Füllrate ist der Anteil der geforderten Einheiten, die sofort ab Lager versandt werden. Als ehemaliger Professor betrachte ich das Service-Level als Alles-oder-Nichts-Note: Wenn ein Kunde 10 Einheiten benötigt und Sie nur 9 bereitstellen können, ist dies eine F. Die Füllrate ist eine Teilkreditnote: 9 von 10 beträgt 90%.
Wenn Sie sich für die Werte von Bestandskontrollrichtlinien entscheiden, finden Sie ein Gleichgewicht zwischen Kosten und Service. Sie können perfekten Service bieten, indem Sie ein unendliches Inventar führen. Sie können die Kosten auf Null halten, indem Sie kein Inventar führen. Sie müssen einen vernünftigen Ort finden, um zwischen diesen beiden lächerlichen Extremen zu operieren. Das Generieren und Analysieren von Nachfrageszenarien kann die Konsequenzen Ihrer Entscheidungen quantifizieren.
Eine Demonstration der Unterschiede zwischen zwei Bestandskontrollrichtlinien
Wir zeigen nun, wie sich der Lagerbestand unter zwei Richtlinien unterschiedlich entwickelt. Die beiden Richtlinien sind (R, Q) und (Min, Max), wobei Rückstände zulässig sind. Um den Vergleich fair zu halten, setzen wir Min = R und Max = R + Q, verwenden eine feste Vorlaufzeit von fünf Tagen und unterziehen beide Policen über 365 simulierte Betriebstage der gleichen Abfolge von Tagesanforderungen.
Abbildung 1 zeigt den täglichen Lagerbestand unter den beiden Policen, die dem gleichen Muster der täglichen Nachfrage unterliegen. In diesem Beispiel hat die (Min, Max) -Richtlinie nur zwei Perioden mit negativem Inventar während des Jahres, während die (R, Q) -Richtlinie drei hat. Die Richtlinie (Min, Max) arbeitet auch mit einer kleineren durchschnittlichen Anzahl verfügbarer Einheiten. Unterschiedliche Nachfragesequenzen führen zu unterschiedlichen Ergebnissen, aber im Allgemeinen schneidet die Richtlinie (Min, Max) besser ab.
Beachten Sie, dass die Diagramme des vorhandenen Inventars Informationen enthalten, die zur Berechnung von Kosten- und Verfügbarkeitsmetriken erforderlich sind.
Abbildung 1: Vergleich des täglichen Lagerbestands unter zwei Bestandsrichtlinien
Rolle der Bestandsplanungssoftware
Best-of-Breed-Systeme für die Bestandsplanung, -prognose und -optimierung können Ihnen dabei helfen, festzustellen, welche Art von Richtlinie (ist es besser, Min / Max über R, Q zu verwenden) und welche Eingaben optimal sind (dh was sollte ich für Min und Max eingeben). Best-of-Breed-Bestandsplanungs- und Bedarfsprognosesysteme können Ihnen dabei helfen, diese optimierten Eingaben zu entwickeln, damit Sie Ihre ERP-Systeme regelmäßig mit genauen Nachschubtreibern füllen und aktualisieren können.
Zusammenfassung
Wir haben die drei am häufigsten verwendeten Bestandskontrollrichtlinien definiert und beschrieben: (T, S), (R, Q) und (Min, Max) sowie die beiden häufigsten Reaktionen auf Lagerbestände: Nachbestellungen oder verlorene Bestellungen. Wir haben festgestellt, dass diese Politiken sukzessive größere Anstrengungen zur Umsetzung erfordern, aber auch sukzessive eine bessere durchschnittliche Leistung aufweisen. Wir haben die Rolle von Bedarfsprognosen bei der Bewertung von Bestandskontrollrichtlinien hervorgehoben. Schließlich haben wir veranschaulicht, wie die Wahl der Richtlinie das tägliche Niveau des Lagerbestands beeinflusst.
Leave a Reply