Was ist Lean Logistics?
Maximierung des Kundennutzens und Beseitigung von Verschwendung
Lean Thinking ist eine Geschäftsmethodik, die in den späten 1980er Jahren in der japanischen Automobilindustrie entstand. Die Kernidee ist es, den Kundennutzen zu maximieren und gleichzeitig Abfälle aus allen Prozessen zu eliminieren. Einfach ausgedrückt bedeutet Lean, mit weniger Ressourcen mehr Wert für Ihre Kunden zu schaffen.
Auch in der Logistik hat Lean Einzug gehalten. Das Konzept ist als Lean Logistics bekannt und hat sich zu einem beliebten Begriff im Supply Chain Management entwickelt.
Lean Logistics definiert
In der Logistikbranche ist Lean einfach eine Möglichkeit, verschwenderische Aktivitäten in der Lieferkette zu erkennen und zu eliminieren. Ziel ist es, den Produktfluss und die Geschwindigkeit zu erhöhen.
Bei Lean Logistics geht es darum, den Betrieb auf allen Ebenen zu verbessern und die Lieferkette durch Reduzierung von Abfall zu optimieren, was für die Kontrolle der Lieferkette wichtig ist. Dies wird durch eine bessere Bestands- und Materialverwaltung sowie durch den Wegfall unnötiger Lieferschritte erreicht, wie z:
-
Minimierung der Bestände / Beseitigung von Überbeständen
-
Minimierung des Transports von “Luft” (Transportressourcen sollten so weit wie möglich gefüllt werden)
Ein schlanker Logistikansatz ist kein Programm oder kurzfristiges Kostensenkungsprogramm. Es handelt sich vielmehr um eine Vorgehensweise zur Beseitigung von Verschwendung entlang ganzer Wertströme, bei der das ultimative Ziel darin besteht, dem Kunden einen perfekten Wert zu bieten.
Die vier Prinzipien der Lean Logistics
-
Wert angeben: Kundennutzen wird entlang des gesamten Supply-Chain-Netzwerks identifiziert und hinzugefügt.
-
Abbildung des Wertstroms: Identifizierung aller Prozesse entlang des Lieferkettennetzwerks, um die Prozesse zu eliminieren, die keinen Wert für das Gesamtprodukt schaffen. Die Abbildung des Wertstroms ermöglicht es Ihnen, Lücken in Ihren Prozessen zu identifizieren. Sie erhalten ein klares Bild davon, wo die Verzögerungen, die Beschränkungen und übermäßigen Lagerbestände liegen. Dies hilft Ihnen zu verstehen, wie der Wert in das Produkt geschaffen wird, aus der Sicht des Kunden.
-
Erstellen eines Produktflusses: Die Anwendung der oben genannten Faktoren und die wertschöpfenden Schritte erfolgen in enger Reihenfolge. Dadurch fließt das Produkt reibungslos zum Kunden, während Unterbrechungen, Lagerbestände und Ausfallzeiten minimiert werden.
-
Ein Pull-System ist ein Produktions- oder Serviceprozess, der darauf ausgelegt ist, den Lagerbestand zu minimieren, indem er direkt auf der Grundlage der Kundennachfrage arbeitet. Waren werden so geliefert, wie sie vom Kunden benötigt werden. Dies wird auch als “Just in Time” -System bezeichnet, da es just in Time arbeitet, um Waren zu liefern, wenn sie benötigt werden, anstatt Inventar anzusammeln. Das Pull-System erfordert, dass Nachfrageinformationen in der gesamten Lieferkette verfügbar sind.
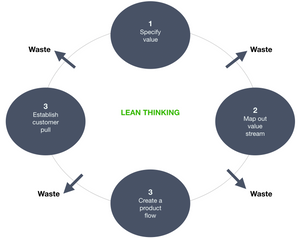
In: Womack, James P. 1996: Lean Thinking (Lean Thinking)
Um eine schlanke Logistik zu erreichen, starten Sie den obigen Prozess erneut und fahren Sie fort, bis ein Zustand der Perfektion erreicht ist, in dem perfekter Wert ohne Verschwendung geschaffen wird.
Fazit
Auf dem heutigen Markt setzen Logistikunternehmen auf Lean-Initiativen, um Verschwendung und Ineffizienzen aufzudecken und zu bewältigen. Die Implementierung von Lean Logistics in Ihr Unternehmen bringt erhebliche Verbesserungen nicht nur für einen bestimmten Bereich der Lieferkette, sondern für die gesamte Wertschöpfungskette als Ganzes. Es ermöglicht Ihnen, auf sich schnell ändernde Verbraucheranforderungen mit höherer Qualität, geringeren Kosten, geringerem Bedarf an Betriebskapital und schnelleren Durchlaufzeiten zu reagieren.
Leave a Reply