Comment Renforcer les Pièces Imprimées en 3D
La Fabrication additive gagne progressivement en inertie dans les différentes branches de l’industrie. Cependant, l’un des principaux obstacles est l’endurance et la performance des pièces – la nécessité de renforcer les pièces imprimées en 3D est primordiale. Étant donné que le matériau le plus couramment utilisé dans les imprimantes 3D est une forme de polymère ou de plastique, les limites du type de pièces pouvant être fabriquées par le procédé et leur durabilité sont là pour tous. Heureusement, il y a eu un certain nombre de développements récents et de possibilités futures en matière de fabrication de pièces plus solides – capables de rivaliser et de rivaliser avec les pièces en acier et en composite. La possibilité de renforcer les pièces imprimées en 3D ajouterait une toute nouvelle couche de valeur au processus d’impression 3D.
Nouveaux procédés de Fabrication additive :
Les premiers efforts de renforcement des pièces imprimées en 3D ont porté sur l’utilisation simple de matériaux à haute résistance, et donc l’adaptation des imprimantes 3D aux exigences d’un tel dépôt. Le SLS (il existe également d’autres procédés) est une méthode utilisée en fabrication additive pour fournir des pièces à haute résistance et construire des composants dans des conditions de travail très sollicitées. Ces procédés sont disponibles dans le commerce dans différentes entreprises et sont connus sous les noms de SLM (Fusion Laser Sélective), EBM (Fusion par faisceau d’électrons) et DMLS (Frittage Laser Direct des métaux). Ils s’appuient sur une méthode de dépôt de poudre pour étaler des couches de poudre et construire des couches qui sont liées ou fondues ensemble.
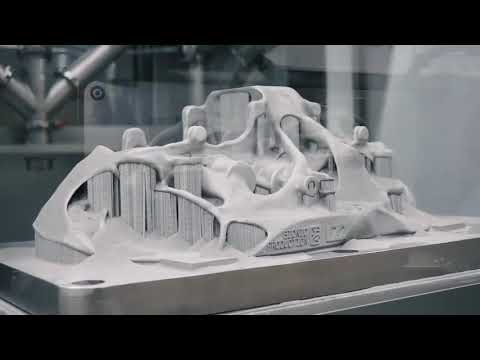
Ces procédés sont cependant très coûteux et exigeants en termes de ressources et de consommation d’énergie. De plus, leur utilisation reste limitée à quelques composants compte tenu de la complexité de l’inspection des pièces et des protocoles d’analyse coûteux, voire indisponibles pour celles-ci (requis à des fins de certification et de test).
Renforcement des fibres:
Depuis l’essor des composites, “tout va mieux avec une poignée de fibres jetées” est devenu une tendance depuis un certain temps. Par conséquent, jeter de courtes fibres de carbone dans la résine de l’imprimante 3D était une évolution compréhensible. Après tout, la résine agira comme une matrice et les fibres fourniront les propriétés mécaniques souhaitées dans une pièce solide. Inutile de dire que beaucoup ont appris à leurs dépens que non, jeter une poignée de fibres de carbone / verre longues et, pire encore, courtes dans le chaudron n’améliorera pas vos pièces. En tout cas, ils peuvent s’avérer désastreux en raison de la négligence de l’anisotropie de ces composants et de l’ignorance de la quantité de calculs et d’études qu’ils nécessitent avant de les inclure dans un composite et de les structurer dans une utilisation spécifique. Des recherches sur la micromécanique des couches et la dynamique des fluides de la résine renforcée sont en cours pour vérifier la prévisibilité de l’orientation des fibres et de leurs propriétés dans le processus FDM.
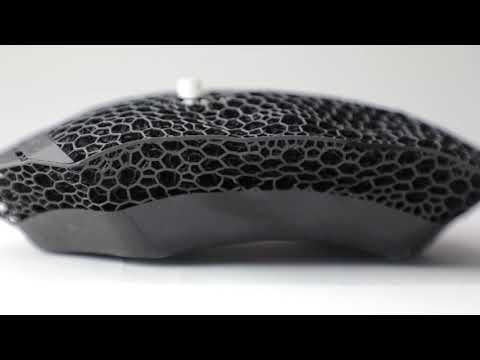
Routage des fibres:
Il existe un moyen plus éclairé d’inclure des fibres dans une pièce imprimée en 3D: soit par le biais de certaines marques d’imprimantes 3D qui permettent à l’utilisateur de choisir le routage des fibres et donc l’orientation lors de la construction des couches, soit par la composition manuelle en remplissant une coque imprimée en 3D de la pièce souhaitée. Ces deux méthodes sont largement utilisées par les amateurs. Bien que ces méthodes puissent donner des résultats satisfaisants, elles nécessitent un post-traitement intensif et ne sont pas utilisées sur des pièces à grande échelle, et encore moins à des fins industrielles.
Adaptation des pièces:
À l’occasion, une révision complète du modèle des pièces sera nécessaire lorsqu’il sera soumis à une trancheuse. De la reconsidération des formes à la mise à l’échelle de la géométrie et à la modification de certaines caractéristiques, il existe plusieurs astuces pour l’impression 3D. Pour s’assurer qu’une pièce est solide toute seule, elle sera soit assemblée à l’aide de supports, soit traitée avec de la chaleur et un revêtement spécial. Ces processus sont les plus couramment utilisés actuellement et impliquent qu’il reste encore du travail à faire pour encourager une utilisation généralisée de la MA.
Même si des recherches sont en cours sur l’aspect viscoélastique de l’écoulement des moisissures, l’orientation des fibres courtes et le degré de contrôle que nous pouvons y avoir, des résultats prometteurs ont été obtenus. Très bientôt, nous pourrons peut-être automatiser l’ensemble du processus et arriver à une situation où le déversement d’une poignée de fibres de carbone courtes dans la machine entraînera une orientation adéquate dans une pièce imprimée en 3D. Bien qu’il reste encore beaucoup de travail à faire, il ne fait aucun doute que le processus nécessaire pour renforcer les pièces imprimées en 3D va dans la bonne direction.
En savoir plus sur l’impression 3D:
- Meilleure imprimante 3D de moins de 1000
- Les Différences Entre Le Métal et Le Métal. Impression 3D plastique
- Impression 3D avec Poudres métalliques
- Nouvelle Technologie révolutionnaire d’impression 3D métallique (Fusion sélective à base de LED)
- Aperçu du logiciel d’impression 3D
- Huile de cuisson usagée de McDonalds: un matériau durable pour l’impression 3D
- Prix, technologie et matériaux d’impression 3D Markforged Metal X
Leave a Reply