Top3Most Common Inventory Control Policies
このブログでは、最も一般的に使用される三つの在庫管理ポリシーを定義し、比較しています。 それは分野に新しいそれらにまた彼らの会社の方針の可能な変更を熟視するベテランの人々に有用であるべきである。 このブログでは、需要予測が在庫管理をどのようにサポートするか、使用するポリシーの選択、およびこれらのポリシーを駆動する入力の計算についても 在庫101の省略された部分としてそれについて考えなさい。
シナリオ
特定のアイテムを管理しています。 項目はあなたがストッキングを避けるために十分な目録を運びたいと思うことあなたの顧客に十分に重要である。 しかし、アイテムはまた、あなたはまた、在庫に縛ら現金の量を最小限に抑えたいことを十分に高価です。 補充在庫を発注するプロセスは、生成する必要がある発注書の数を最小限に抑えたいほど、十分に高価で面倒です。 アイテムの需要は予測不可能です。 従って多くのための必要性を検出するときと使用または郵送物の準備ができた棚で着くとき間の補充の調達期間はある。
あなたの質問は、”このアイテムを管理するにはどうすればよいですか? どのように私はより多くを注文するときに、どのくらい注文するかを決定するのですか?”この決定を下すとき、あなたが使用できるさまざまなアプローチがあります。 このブログでは、最も一般的に使用される在庫計画ポリシーの概要を説明します:定期注文(T、S)、再注文ポイント/注文数量(R、Q)、および最小/最大(s、S)。 これらのアプローチは、多くの場合、ERPシステムに埋め込まれており、何を注文するときの自動提案を生成するために企業を可能にします。 適切な判断を下すには、これらの各アプローチがどのように機能するように設計されているか、および各アプローチの利点と制限を知る必要があります。
定期的なレビュー、order-up-to policy
このポリシーの省略表記は(T,S)で、Tは注文間の固定時間、Sは注文-up-to-levelです。
ご注文のタイミング:注文はT日ごとに時計仕掛けのように配置されます。 固定再注文間隔の使用は、在庫レベルをリアルタイムで追跡できない企業や、予定された間隔でサプライヤーに注文を発行することを好む企業に役立
注文する量:在庫レベルが測定され、そのレベルと注文までのレベルSとの間のギャップが計算されます。在庫レベルが7単位でS=10の場合、3単位が注文されます。
コメント:これは、実装するのが最も簡単なポリシーですが、需要および/またはリードタイムの変動に対応する上で最も機敏ではありません。 また、補充が即時であれば、注文サイズは在庫レベルをSに戻すのに十分であるが、実際には在庫が低下し続ける間に補充遅延が発生するため、在庫レベルがsまで到達することはめったにないことに注意してください。
継続的なレビュー、固定注文数量ポリシー(再注文ポイント、注文数量)
このポリシーの省略表記は(R,Q)であり、Rは再注文ポイント、Qは固定注文数量です。
ご注文のタイミング: 理論的には、在庫レベルは常にチェックされますが、実際には通常、各作業日の開始または終了時に定期的にチェックされます。
注文する量:注文サイズは常にQ単位で固定されています。
コメント:(R,Q)は(S,T)よりも反応性が高い。 固定注文数量Qの値は、完全にあなた次第ではないかもしれません。 多くの場合、サプライヤーは、Qの選択を最小値および倍数と互換性のある値に制限する用語を指示することができます。 たとえば、仕入先は最低20単位の注文を要求し、常に5の倍数にすることができます。 したがって、注文サイズは20、25、30、35などのいずれかでなければなりません。 (このコメントは、他の二つの在庫ポリシーにも適用されます。)
継続的なレビュー、注文アップアップポリシー(最小/最大)
このポリシーの省略表記は(s、S)で、”little s、big S”と呼ばれることもあ このポリシーは、より一般的に(Min,Max)と呼ばれます。
注文時期:在庫が最小値以下に低下するとすぐに注文が行われます。 (R,Q)と同様に、在庫レベルは常に監視されていると思われますが、実際には通常、各作業日の終わりにチェックされます。
: 注文サイズは異なります。 これは、最小値に達するか、または違反した瞬間の最大値と現在の在庫との間のギャップに等しくなります。
コメント:(Min,Max)は、在庫が最小値を下回っていることを考慮して注文サイズを調整するため、(R,Q)よりもさらに応答性が高くなります。 需要がゼロまたは一つの単位のいずれかである場合、共通の変動はMin=Max-1を設定します。”
もう一つの政策選択:在庫切れの場合はどうなりますか?
ご想像のとおり、各ポリシーは、在庫レベルの異なる一時的なシーケンスにつながる可能性があります(下の図1を参照)。 時間の経過とともにイベントがどのように再生されるかに影響を与えるもう一つの要因があります:在庫切れに対処するために選択したポ 大まかに言えば、2つの主要なアプローチがあります。
バックオーダーポリシー:在庫切れの場合は、注文を追跡し、後で記入します。 この政策の下では、負の在庫について話すことが賢明です。 負の在庫は、記入する必要があるバックオーダーの数を表します。 おそらく、待機を余儀なくされた顧客は、補充が到着したときに最初のdibsを取得します。 あなたの顧客が他の場所で購入することはできませんあなたのビジネスに固有のアイテムのバックオーダーポリシーを持っている可能性があります。
損失ポリシー:在庫切れの場合、顧客は注文を満たすために別のソースに変わります。 補充が到着すると、いくつかの新しい顧客は、それらの新しいユニットを取得します。 在庫はゼロ以下になることはありません。 競合他社から簡単に購入できる商品アイテムについては、このポリシーを選択します。 在庫でそれを持たなければ、あなたの顧客は最も確かに他の所で行く。
在庫管理における需要予測の役割
最小値や最大値などの制御パラメータの選択には、ある種の需要予測プロセスからの入力が必要です。
従来、これは、(R,Q)および(Min,Max)システムのリードタイム、または(T,S)システムのT+リードタイムのいずれか、一定の時間間隔で要求されるユニット数の確率分布を決定することを意味していました。 この分布は正規分布であると仮定されています(有名な「鐘形の曲線」)。 従来の方法は、需要分布が正規分布ではなく、他の分布(ポアソン、負の二項分布など)であると仮定されている場合に拡張されています。)
これらの伝統的な方法論にはいくつかの欠点があります。
- まず、通常、需要が在庫を再注文ポイントだけでなくその下に落とすアンダーシュートの問題を無視します。 アンダーシュートがないと仮定すると、サービスレベルと充填率が過大評価されます。
- 第二に、需要の確率分布は、特にスペアやサービス部品などの断続的な需要がある品目については、”ベル型”または想定される分布が選択されたものに近
- 第三に、在庫運用コストの正確な見積もりには、在庫が再注文ポイントに当たることから始まるサイクルの一部だけでなく、補充サイクル全体(ある補充から次の補充まで)の分析が必要です。
- 最後に、補充リードタイムは通常、予測不可能またはランダムであり、固定されていません。 多くのモデルでは、平均、ベンダー見積リードタイム、または平均リードタイム+安全時間に基づいて固定リードタイムを想定しています。
幸いにも、より良い在庫計画と在庫最適化ソフトウェアは、ランダムなリードタイムとともに、ランダムな需要シナリオの全範囲を生成することに基づ これらのシナリオは、”ストレステスト”在庫管理パラメータの任意の提案されたペアとその期待されるパフォーマ ユーザーはポリシーを選択するだけではありません(つまり、 最小、最大対R、Q)だけでなく、提案されたポリシーのどの変化が最良であるかを決定する(すなわち、最小、最大10,20対15,25など)。)これらのシナリオの例を以下に示します。
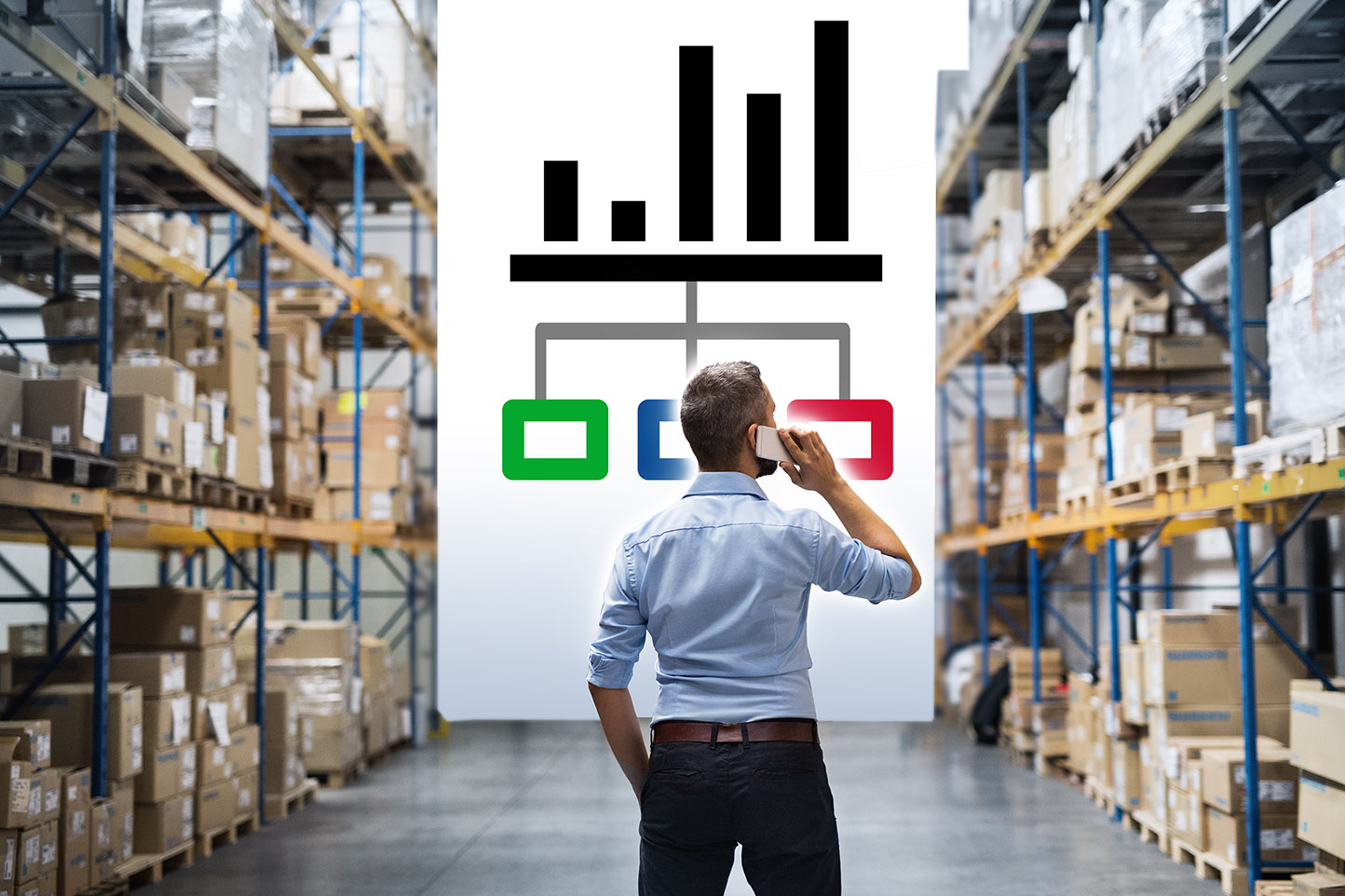
補充在庫を注文するプロセスは十分に高価で面倒であるため、発注書の数を最小限に抑えたい場合は、
在庫管理ポリシーの中から選択する
アイテムの可用性の点で明確な序列があり、(最小、最大)が最初、(R、Q)が2番目、(T、S)が最後です。 この順序は、需要と補充のランダム性の変動に対する政策の応答性に由来する。 実装の容易さを考慮すると、順序は逆になります。
在庫ポリシーのパフォーマンスをどのように”スコア”しますか? コストとサービス:バランスをとる必要があります二つの反対の力があります。
在庫コストは、在庫投資または在庫運用コストのいずれかとして表すことができます。 前者は、使用されるのを待っているアイテムのドル価値です。 後者は3つの部品の合計である:費用(棚の原料の”心配そして供給の費用”)を握ること、費用(基本的に購入指示書を切り、その順序を受け取る費用)、および不足の費用(販売を失うか、または顧客がほしいと思うものを待つように強制するとき支払う罰)を発注する。
サービスは通常、サービスレベルと充填率によって測定されます。 サービスレベルは、要求された品目が在庫からすぐに出荷される確率です。 充填率は、在庫からすぐに出荷される要求される単位の割合です。 元教授として、私はサービスレベルをオールオアナッシンググレードと考えています:顧客が10台を必要とし、9台しか提供できない場合、それはFです。
在庫管理ポリシーの値を決定するとき、コストとサービスのバランスを取っています。 あなたは無限の在庫を維持することによって完璧なサービスを提供することができます。 在庫を保持しないことで、コストをゼロに抑えることができます。 あなたはこれら二つのばかげた両極端の間で動作するように賢明な場所を見つける必要があります。 需要シナリオの生成と分析は、選択の結果を定量化することができます。
二つの在庫管理ポリシーの違いのデモンストレーション
二つのポリシーの下で手持在庫がどのように異なって進化するかを示します。 2つのポリシーは、(R,Q)と(Min,Max)で、バックオーダーが許可されています。 比較を公平に保つために、Min=RとMax=R+Qを設定し、5日間の固定リードタイムを使用し、両方のポリシーに365日間のシミュレートされた運用期間にわたって同
図1は、日次需要のパターンが同じである二つのポリシーの下での日次手持在庫を示しています。 この例では、(Min,Max)ポリシーのマイナス在庫期間は2つだけですが、(R,Q)ポリシーのマイナス在庫期間は3つです。 (最小、最大)ポリシーは、手元のユニットの平均数も少なくても動作します。 需要シーケンスが異なると結果が異なりますが、一般的には(Min,Max)ポリシーの方が優れています。
手持在庫のプロットには、コストと可用性の両方の指標を計算するために必要な情報が含まれていることに注意してください。
図1: 2つの在庫ポリシーに基づく毎日の手持在庫の比較
在庫計画ソフトウェアの役割
ベストオブブリード在庫計画、予測、最適化システムは、どのタイプの Best of breed在庫計画および需要予測システムは、これらの最適化された入力を開発するのに役立ち、正確な補充ドライバーを使用してERPシステムを定期的に移入および更新できるようにします。
概要
私たちは、最も一般的に使用される3つの在庫管理ポリシー(T、S)、(R、Q)、(Min、Max)と、在庫切れに対する最も一般的な2つの応答(backordersまたはlost orders)を定義し、説 我々は、これらの政策を実施するためには、連続的に大きな努力が必要であるが、平均的なパフォーマンスも連続的に良好であることに留意した。 我々は、在庫管理政策を評価する上での需要予測の役割を強調した。 最後に、政策の選択が手持在庫の日々のレベルにどのように影響するかを示しました。
Leave a Reply