Czym jest lean logistics?
maksymalizacja wartości klienta i eliminacja odpadów
Lean Thinking to metodologia biznesowa, która powstała w japońskim przemyśle motoryzacyjnym pod koniec lat 80. głównym założeniem jest maksymalizacja wartości klienta przy jednoczesnym wyeliminowaniu odpadów ze wszystkich procesów. Mówiąc najprościej, Lean oznacza tworzenie większej wartości dla klientów przy mniejszej liczbie zasobów.
Lean również trafił do logistyki. Pojęcie to znane jest jako Lean Logistics I stało się popularnym terminem w zarządzaniu łańcuchem dostaw.
Lean logistics zdefiniowany
w sektorze logistycznym bycie lean jest po prostu sposobem na rozpoznanie i wyeliminowanie marnotrawstwa z łańcucha dostaw. Celem jest zwiększenie przepływu i szybkości produktu.
Lean Logistics to usprawnienie działań na wszystkich poziomach i optymalizacja łańcucha dostaw poprzez zmniejszenie ilości odpadów, co jest ważne dla kontroli łańcucha dostaw. Osiąga się to poprzez lepsze zarządzanie zapasami i materiałami oraz eliminację niepotrzebnych etapów dostawy, takich jak:
-
minimalizacja zapasów / eliminacja nadmiaru zapasów
-
minimalizacja transportu “powietrza” (zasoby transportowe powinny być wypełnione w jak największym stopniu)
podejście lean logistics nie jest programem ani krótkoterminowym programem redukcji kosztów. Jest to raczej sposób działania w celu wyeliminowania odpadów wzdłuż całych strumieni wartości, gdzie ostatecznym celem jest zapewnienie idealnej wartości dla klienta.
cztery zasady lean logistics
-
określanie wartości: Wartość klienta jest identyfikowana i dodawana w całej sieci łańcucha dostaw.
-
mapowanie strumienia wartości: identyfikacja wszystkich procesów w sieci łańcucha dostaw w celu wyeliminowania procesów, które nie tworzą wartości dla całego produktu. Mapowanie strumienia wartości pozwala zidentyfikować luki w procesach. Masz jasny obraz tego, gdzie są opóźnienia, ograniczenia i nadmierne zapasy. Pomaga to zrozumieć, w jaki sposób wartość jest tworzona w produkcie, z perspektywy klienta.
-
tworzenie przepływu produktu: Zastosowanie powyższych czynników i wykonanie etapów tworzenia wartości następuje w ścisłej kolejności. Dzięki temu produkt płynnie dotrze do klienta, a wszystko to przy minimalizacji przerw, zapasów i przestojów.
-
ustanowienie klienta pull: system pull jest procesem produkcyjnym lub usługowym, który ma na celu zminimalizowanie zapasów pod ręką, pracując bezpośrednio na podstawie zapotrzebowania klienta. Towary są dostarczane zgodnie z wymaganiami klienta. Jest to również znane jako system “Just in time”, ponieważ działa na czas w dostarczaniu towarów, gdy są one potrzebne, zamiast gromadzić zapasy. System pull wymaga, aby informacje o popycie były dostępne w całym łańcuchu dostaw.
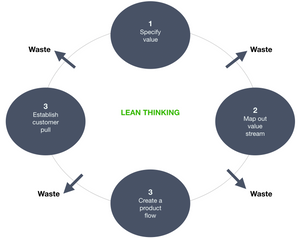
Womack James P., Daniel T. Jones (1996)
aby osiągnąć Lean Logistics, rozpocznij powyższy proces ponownie i kontynuuj, aż do osiągnięcia stanu doskonałości, w którym powstaje doskonała wartość bez marnotrawstwa.
podsumowanie
na dzisiejszym rynku firmy logistyczne podejmują inicjatywy Lean, aby odkrywać i radzić sobie z marnotrawstwem i nieefektywnością. Wdrożenie Lean Logistics w Twojej firmie przynosi znaczące ulepszenia nie tylko w jednym konkretnym obszarze łańcucha dostaw, ale w całym łańcuchu wartości. Umożliwia reagowanie na szybko zmieniające się potrzeby klientów, oferując wyższą jakość, niższe koszty, mniejsze zapotrzebowanie na kapitał obrotowy i szybszy czas przepustowości.
Leave a Reply